
Make two wedges about three-quarters the length of the tenon, and about 3mm (Yqin) thick at the wide point. Having chopped out the mortise, saw the sides of the haunch groove at an angle, taking care not to overrun, then pare the slope with a chisel. When marking out the mortise, continue the gauged lines up to the top of the stile, but not over the end.
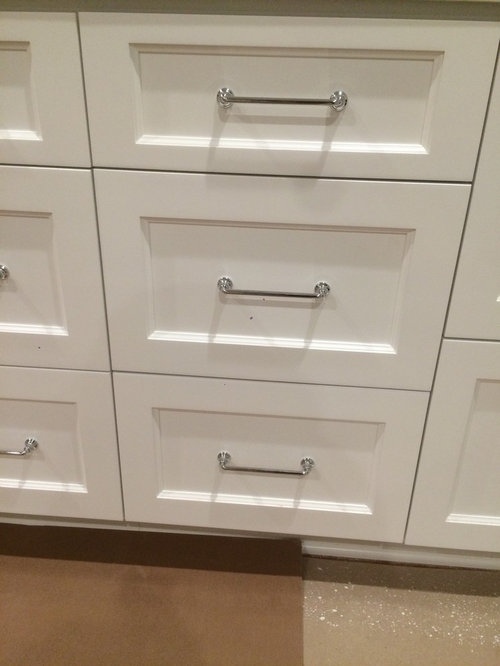
Saw down this line, after first cutting along the top edge of the tenon (see above). Finally, saw along the shoulders to remove waste Mark out the tenon, including the haunch (see opposite), then score the sloping sides of the haunch with a marking knife. Reposition the work and saw down the end of the haunch, forming a notch at the top corner of the joint. clamp the work upright in a vice and saw beside the line marking the top edge of the tenon, down to the haunch. Use a chisel to pare away the waste, leaving the bottom of the groove square. Having cut the mortise (see page 65), extend the sides by sawing along the gauged lines, down to the bottom of the haunch groove. Scribe a short line on the end of the stile to mark the depth of the haunch groove. Scribe the mortise up to the end of the stile, and then continue the lines a short way onto the end grain this marks the end of the haunch groove. This extension, known as the horn, is cut off and planed flush when the joint is complete. At this stage, let the end of the stile project by about 18mm (3/iin) to prevent splitting. Using the rail as a template, mark the position of the mortise on the stile. Mark the length of the haunch across the top and down the sides of the rail, and then hatch the waste with a pencil.


Having marked the shoulders and scribed the tenon thickness on the rail (see page 64), use a marking gauge to scribe the top edge of the tenon on both sides and across the end grain. Make a sloping haunch to the same proportions, but pare it away to meet the shoulder line. Then there is the matter of growing up in a country where we used metric measurements and did not have the challenge to deal with fractions, so my brain is already at a disadvantage to yours.Make the tenon two-thirds the width of the rail the haunch itself should be as long as it is thick. Flat panels I like to use plywood and at least spot glue it into the frame. So there is a coat of finish helping to keep the panel in place too. But I put one more coat on everything after finishing the frame. I also finish the inside of the frame and the panels before glueup and flush up the frame and finish it after glueup. They always have a little friction to keep them from rattling. Maybe it's my wood or glueups but my panels have never been so flat they move freely in the frame. It tends to be drier in the winter than the summer so I might make the minimum engagement 1/16 if building the doors in winter. I usually make the panel so that it will have a minimum 1/8 engagement in the off side groove if it bottom out on the other side. Sometimes I plan on 1/8 clearance all the way around - which often isn't enough but leaves less to trim.

#Stiles and rails proportions plus
The horizontal pieces are the opening width minus the vertical pieces plus two times the cut width of the cope and stick cutters. This extra material can help if things don't turn out just right in either the door or the box. So the rails and stiles may be 1/16 less than I just described when I am done. I often make the doors to fit the opening with no clearance and then trim to fit. I used to use 2 1/4 mostly but we bought the kitchen cabinets we did because my wife liked the 3 inch wide rails and stiles. The width of the rails and stiles is for appearance.
